FAST
Konzeption und Entwicklung von integrierten, innovativen Prozessketten mit extrem schnellen Fertigungszyklen zur Befähigung einer agilen Produktentwicklung und Produktion für die zukünftige hybridelektrische Luftfahrt
Ziel
FAST verfolgt das Ziel, Fertigungstechnologien für Komponenten eines neuen hybrid-elektrischen Antriebs zu beschleunigen und zu agilisieren. Dabei soll mit Hilfe Digitalisierung und Automation die Entwicklungszeit vom CAD bis zum Funktionsprototypen auf weniger als 6 Wochen gesenkt werden. FAST fördert gleichzeitig den Aufbau und die Inbetriebnahme eines digital vernetzten, extrem schnellen Fertigungsnetzwerks (FMERC) für komplexe, hochintegrierte Strukturen eines hybrid-elektrischen Flugantriebs. Durch automatisierte und integrierte Inspektion sowie erweiterte Prozess- und Eigenschaftssimulation soll eine Informationsstruktur für den digitalen Zwilling der Produktion entstehen.
Kurzbeschreibung
Die formulierten Ziele einer umweltfreundlichen Luftfahrt erfordern disruptive Technologiesprünge, die nur durch eine agile, digital vernetzte Produktentwicklung und -fertigung erreicht werden können. Der angepasste Demingzyklus (Definition – Herstellung – Datenaufnahme und -analyse – Optimierung) muss dabei für das Komponentenportfolio eines hybrid-elektrisches Antriebssystems auf ein bisher nicht erreichtes zeitliches Minimum verkürzt werden. Vom Entwurf bis zum verifizierten Prototyp wird ein Zyklus von maximal 8 Wochen angestrebt. Um diese Zyklenzeiten zu erreichen, erarbeitet FAST die Prozessketten und operative Struktur einer hochintegrierten, adaptiven und extrem schnellen Vorserienfabrik. Der primäre Fokus liegt in der Entwicklung hocheffizienter additiver wie subtraktiver Fertigungsketten und deren Kombination. Plattform-, Modulstrategien und „Rapid Tooling“ Techniken sollen den Werkzeug- und Vorrichtungsaufwand von Um-, Urform-, Fügeprozessketten minimieren und somit etablierte Fertigungs- und Montageverfahren beschleunigen. Durch eine automatisierte und integrierte zerstörungsfreie Inspektion werden Qualität und Geometrie verifiziert. Die agile Vorserienfertigung muss dabei eine hohe werkstoffliche und geometrische Adaptionsfähigkeit aufweisen. Ein verknüpftes, digitales Daten- und Informationsmanagement entlang des Demingzyklus stellt einen verlustfreien und schnellen Dateninput und -output sicher. Um die Datenaufnahme zu vereinheitlichen und Informationen zu maximieren, werden die relevanten Prozessparameter und -outputs eines jeden Zyklus oder Experiments in einer „Werkstoff-Prozess-Eigenschafts“ DNA gespeichert. Die Definition und Optimierung der relevanten Prozesse und ihrer Einflussgrößen erfolgt anhand der DNA der physischen Fertigungszyklen unterstützt durch eine durchgehende Werkstoff-Prozess-Modellierung. Durch digitale Datenanalyse werden die Prozessketten hinsichtlich Zeit, Flexibilität und Robustheit kontinuierlich verbessert.
Projektpartner
Brandenburgische Technische Universität Cottbus-Senftenberg ,Fraunhofer-Institut für Werkzeugmaschinen und Umformtechnik ,Rolls-Royce Deutschland Ltd Co KG,Schaeffler Aerospace Germany GmbH Co. KG
Ansprechpartner/in
Dr. Matthias Bünck
+49 241 943249 34
m.buenck@access-technology.de
Projektinformationen
Laufzeit
9/1/22 –
8/31/26
Förderkennzeichen
20L2105C
Zuwendungsgeber
Bundesministerium für Wirtschaft und Klimaschutz (BMWK)
Projektträger
Deutsches Zentrum für Luft- und Raumfahrt e. V. (DLR)
Förderinitiative
LuFo-VI-2
Geschäftsfeld
Prozessentwicklung und Prototypenfertigung
Projektstatus
in Bearbeitung
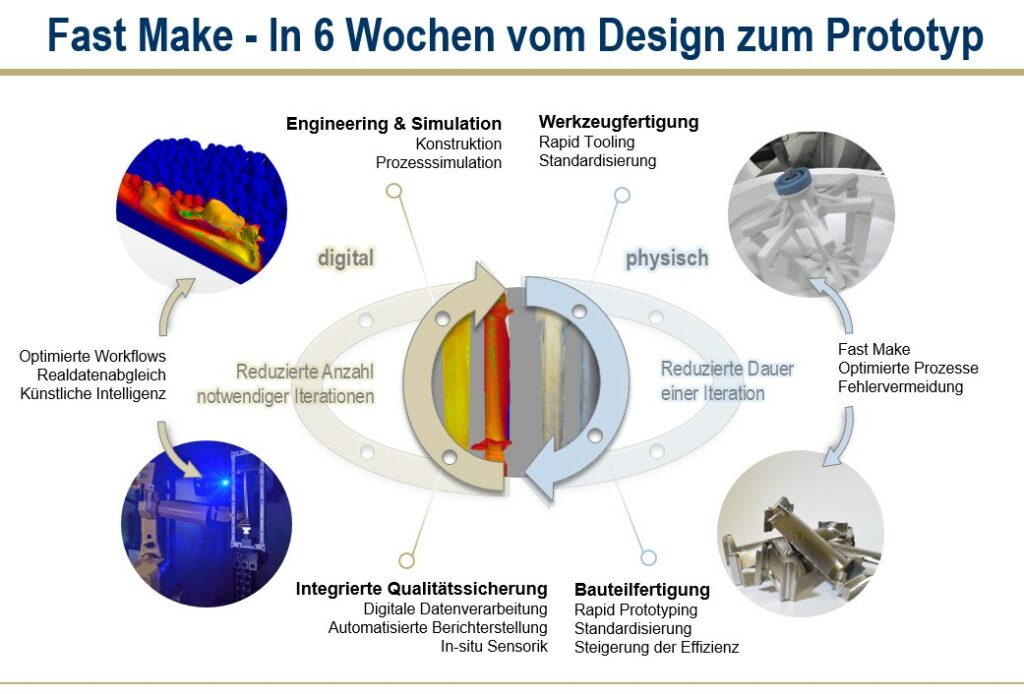