Material characterization
- Susanne Hemes
- +49 241 80 98021
- s.hemes@access-technology.de
Material characterization: properties, phases, shape and microstructure (microstructural analysis)
A comprehensive and quantitative assessment of material and component properties is one of Access’ core competencies. Both as support for our publicly funded projects, as well as in the context of industrial projects and in the form of contract work for our external customers.
Thematically, the focus is on the documentation and quantification of morphology, texture development and the control of phase proportions, grain and phase interfaces and other characteristics of the properties of a material.
State-of-the-art equipment and software are available for the characterization of microstructure and material properties, as well as numerical models and simulation tools. Spread across three laboratories, Access e.V. focuses on microscopy, computed tomography and characterization of mechanical properties.
Phases, structure, properties, chemistry, form
Structure
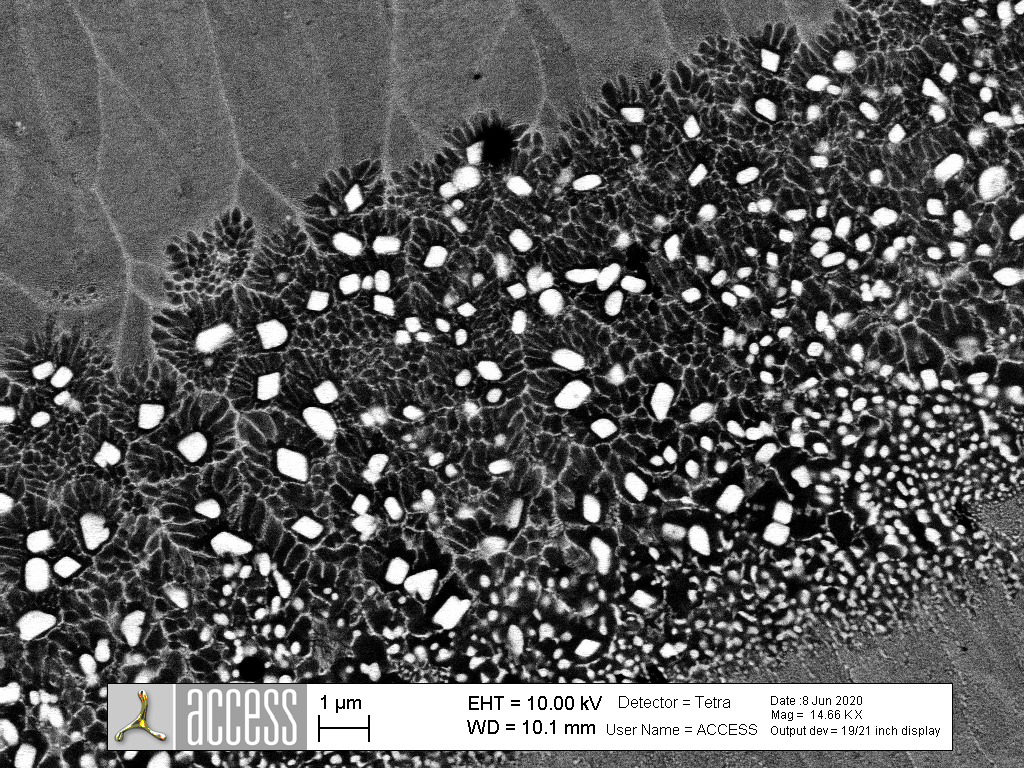
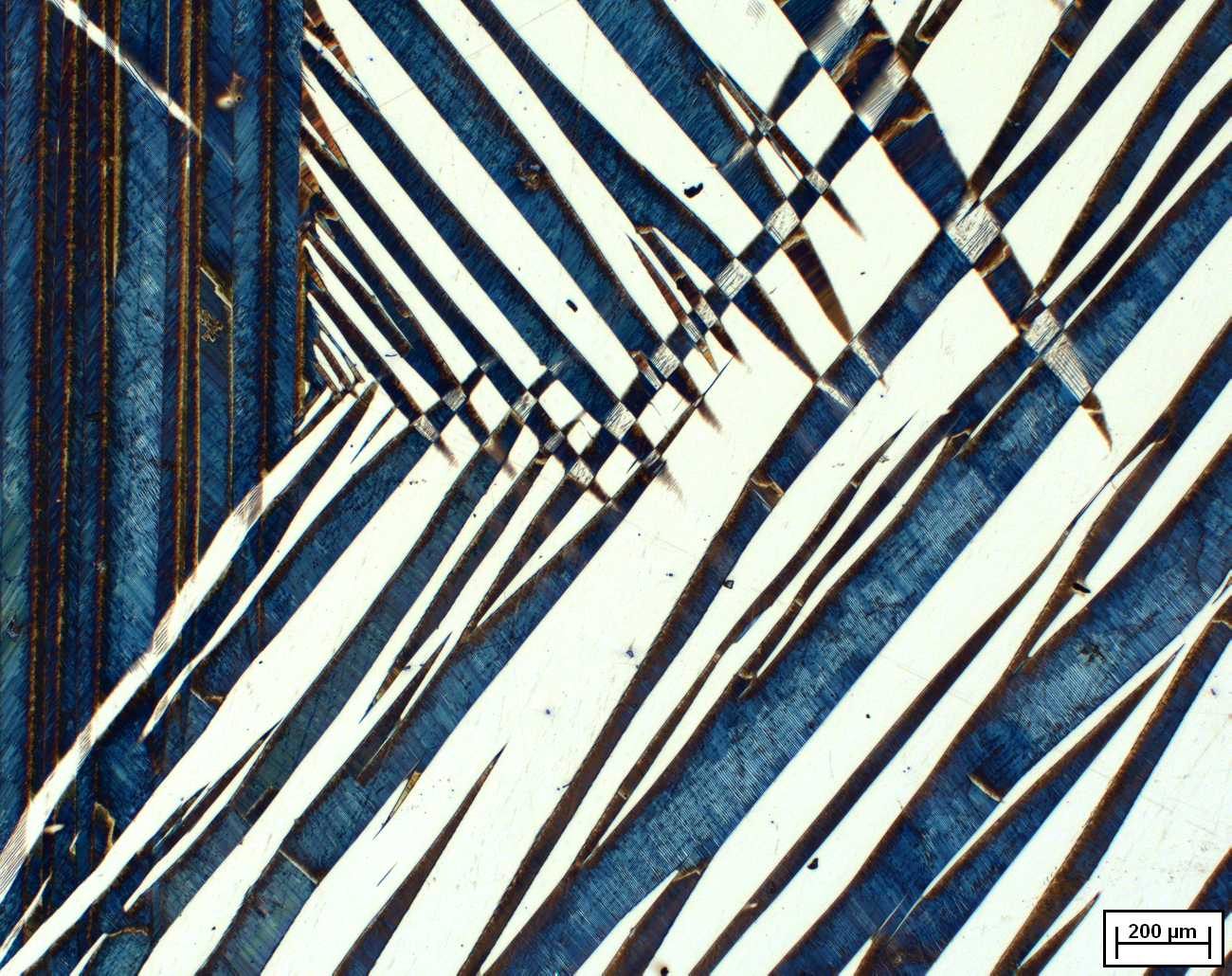
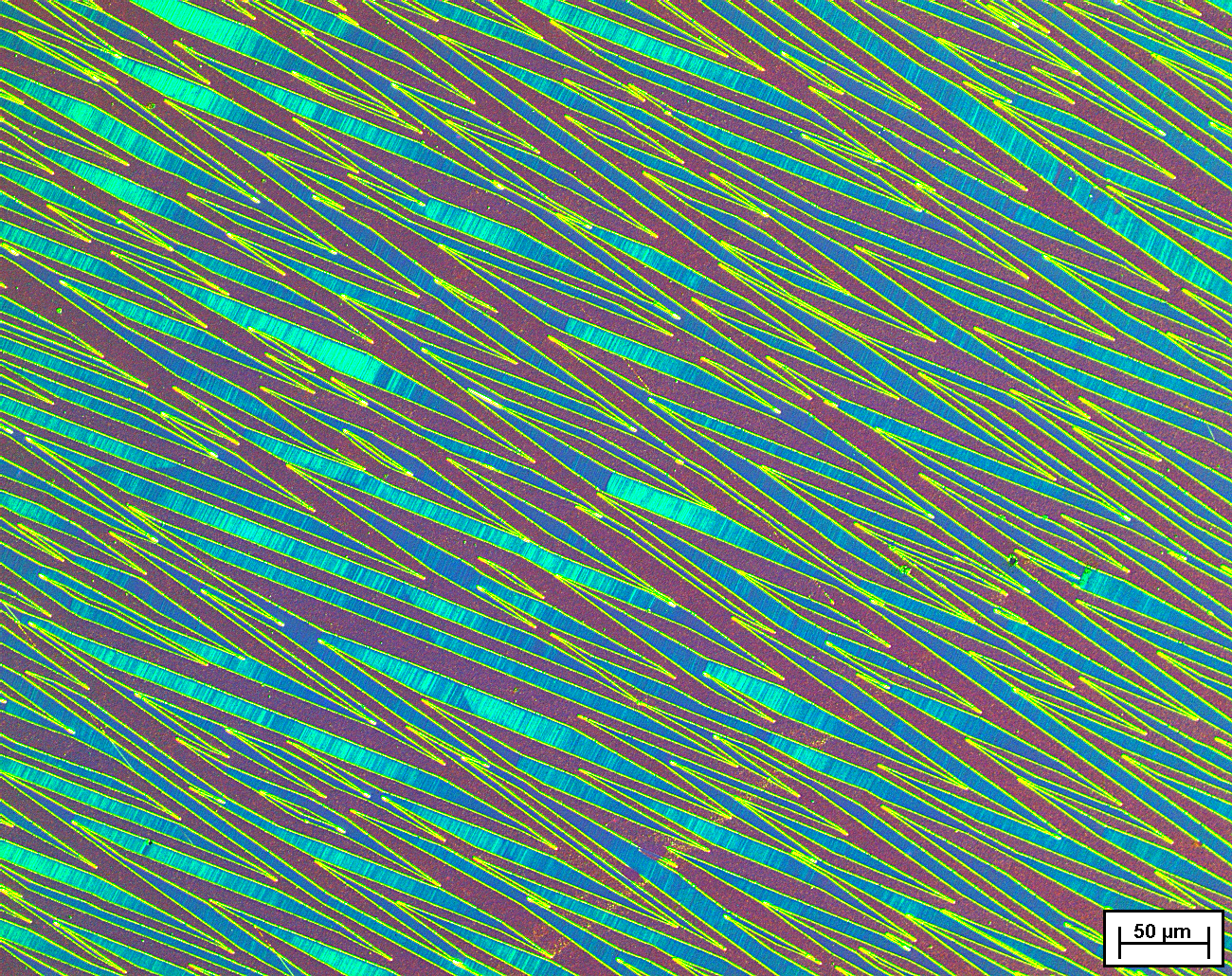
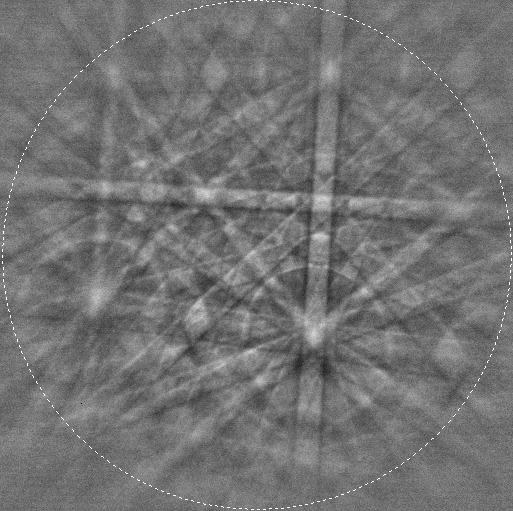
Microstructure and microstructural characterization are primarily carried out using:
- Three Zeiss field emission scanning electron microscopes (ULTRA55, 1540XB and LEO1550), equipped with Oxford EDX systems (UltimMax 170, X-MaxN 150 and INCA X-act) for elemental analysis and phase analysis, as well as EBSD systems (Nordlys), for the determination of crystallographic orientations and grain size distributions and for texture analysis, with a resolution down to the nm range.
- Zeiss light microscopes are used for microstructure and grain size analysis, and a digital HIROX light microscope for surface roughness measurement and profile analysis, as well as defect characterization and monitoring of miniature tensile tests and 3-point bending tests.
- An atomic force microscope TOSCA (AFM) is used for the 3D characterization of surfaces and is particularly suitable for nano- and micrometer-structured materials. In magnetic force microscopy mode, magnetically different phases within a material can also be characterized. For soft materials (e.g. polymers), nanomechanical properties can be determined by indentation.
Access e.V. is used to determine the 3D microstructure and component properties:
- An industrial Nikon CT, which allows the non-destructive imaging of the volume properties of a component with a resolution down to the micrometer range. Modular X-ray sources from 225-320kV enable the imaging of structure sizes down to 15 µm, with a detector from Perkin Elmer, which has a 16-bit gray scale resolution. A walk-in sample chamber also allows the installation of large samples.
- An ATOS Scan-Box 5108 is used to create high-resolution 3D scans of components up to 80 cm in size. With a robot arm-guided measuring head, the scan box is particularly suitable for 3D scans of turbine blades, turbochargers, blisks and cast housings. For airfoil inspections, sharp radii can be recorded in position and contour with a detail resolution of more than 20 measuring points per millimeter.
- Software packages such as Volume Graphics or Polyworks are tailored to the respective application, also in combination with each other, and the three-dimensional results of volume and surface analyses are combined – depending on the problem – and converted into FE meshes for simulation, for example.
Geometry, 3D metrology and NDT
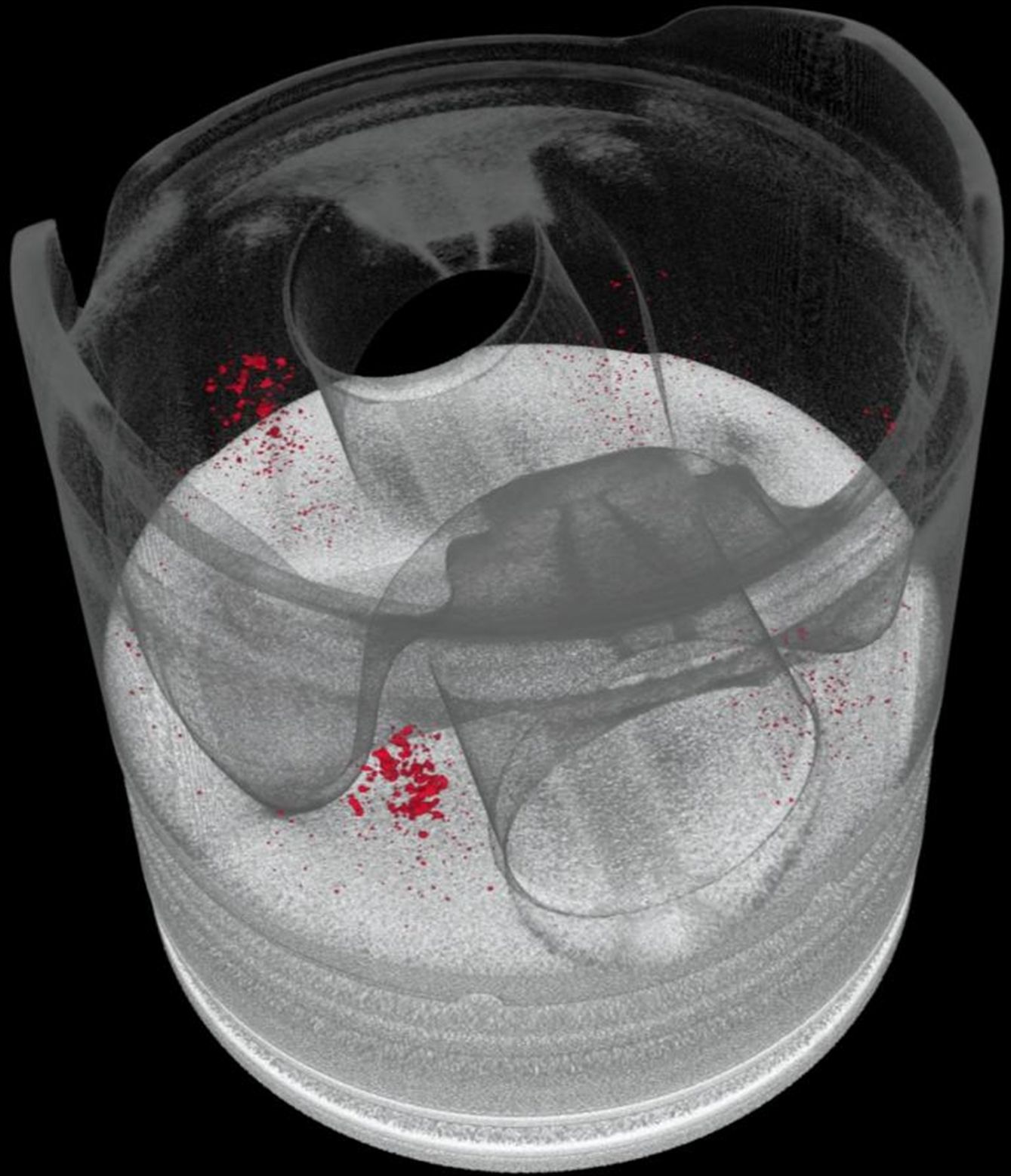
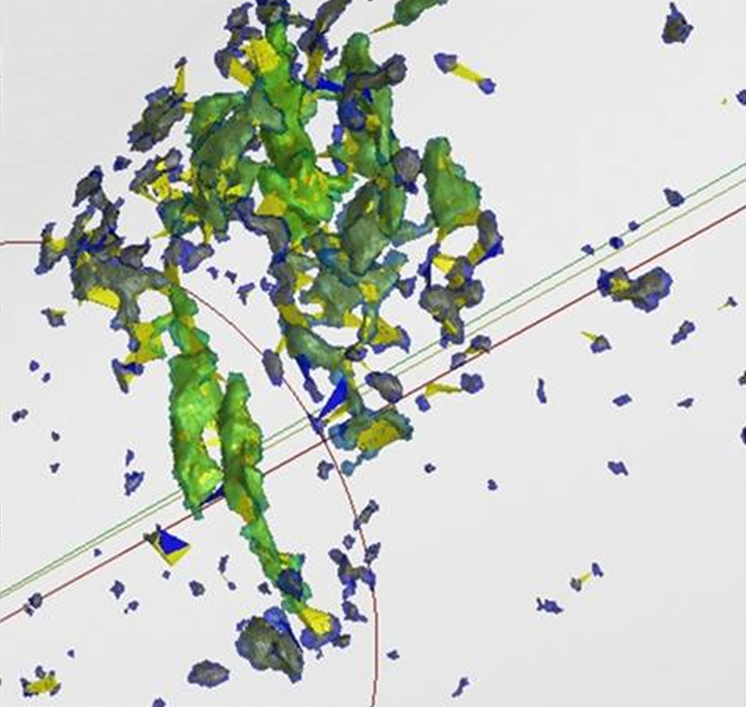
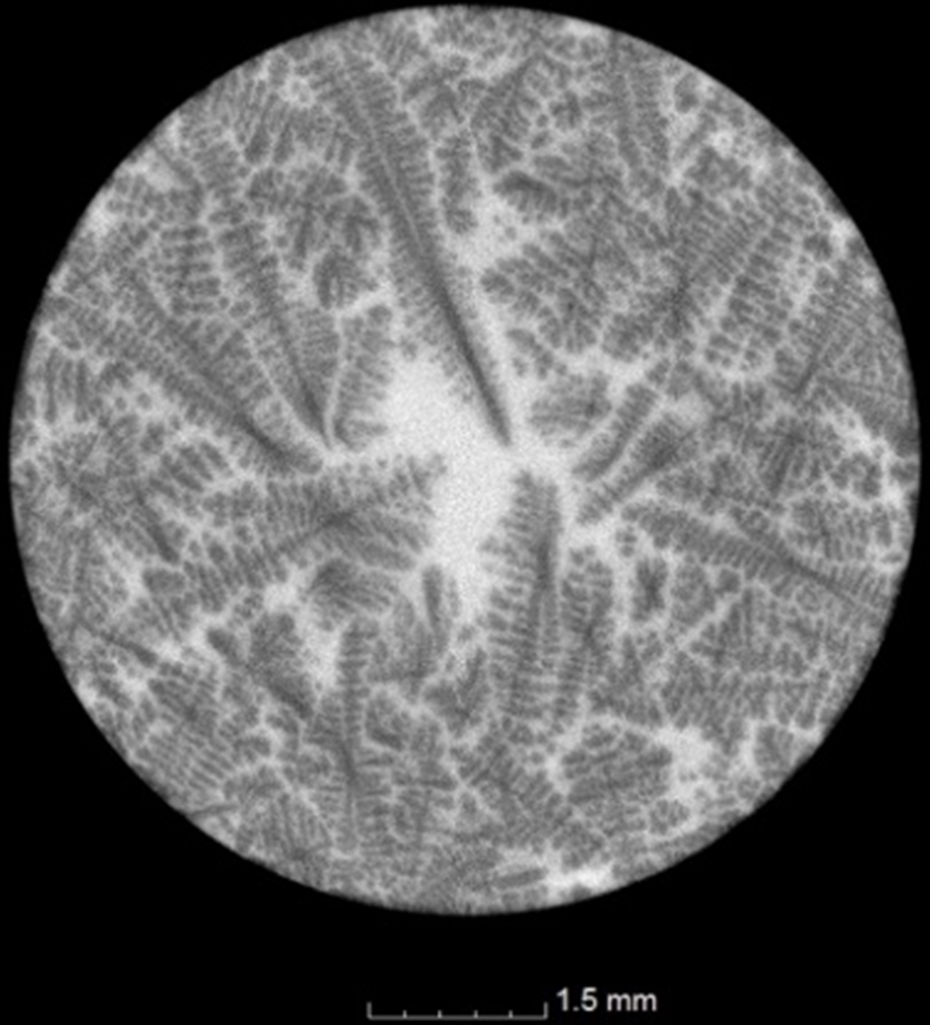
Properties
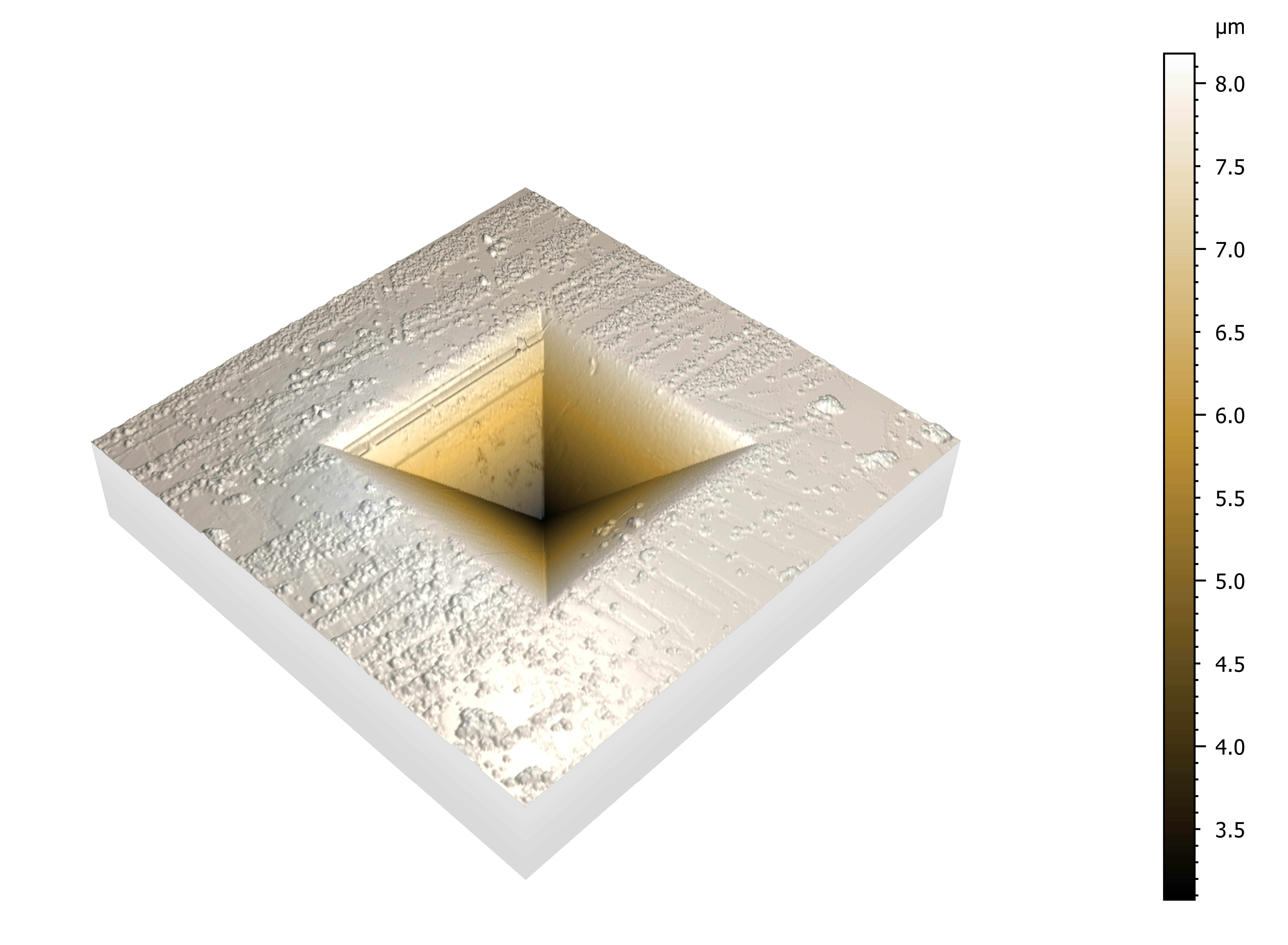
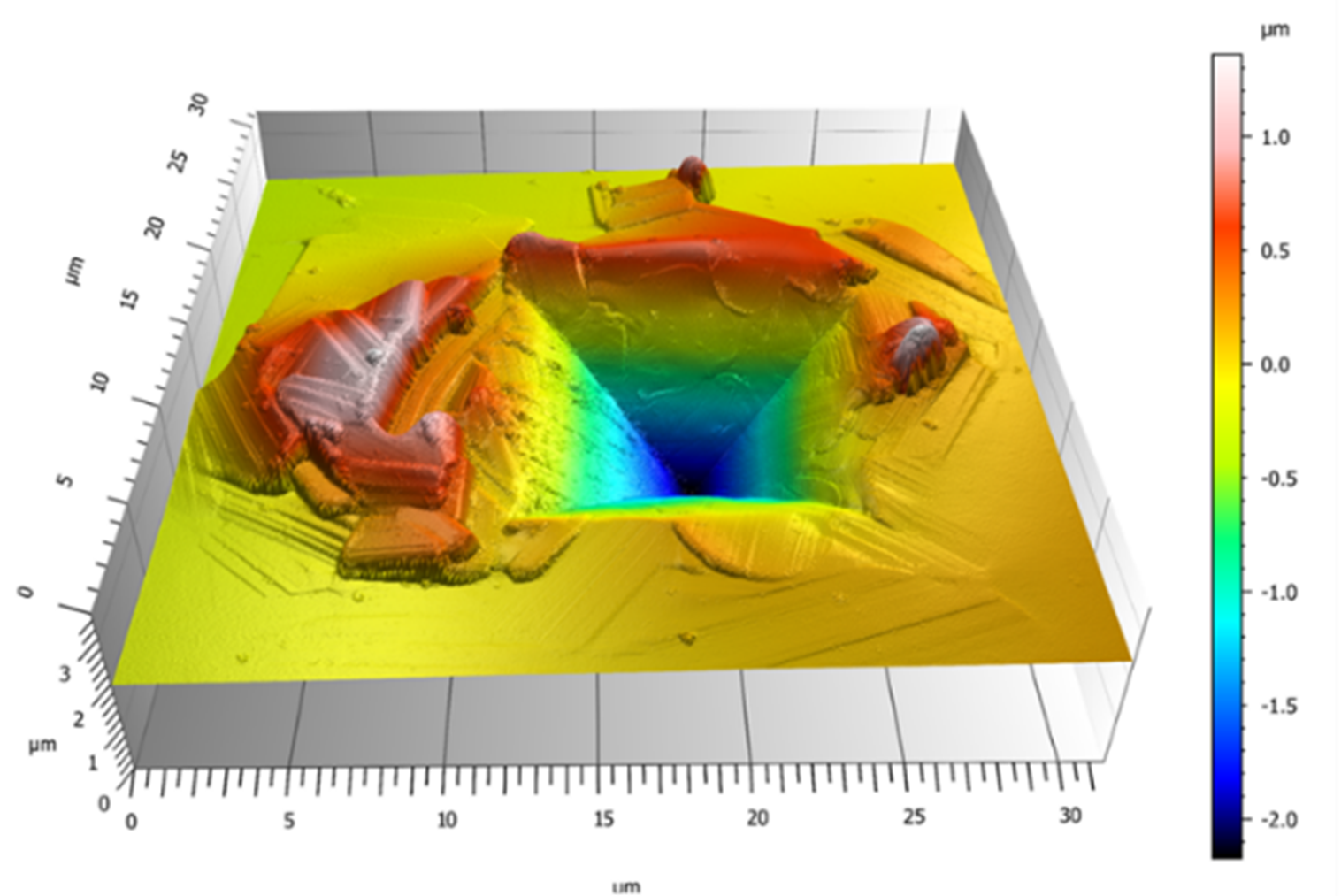
The mechanical properties of a material can be analyzed by means of:
- Tribometry, for the analysis of wear properties and abrasion,
- fatigue tests to determine the fatigue properties – also on miniature test specimens,
- Miniature tensile (tensile strength measurement) and 3-point bending tests to determine the flexural strength and plastic strain of a material,
- as well as high-temperature tensile tests and creep tests (Zwick-Roell).
The instrumented micro-hardness test is used to measure the hardness and to determine the modulus of elasticity and work hardening of a material.