Process simulation
- Jürgen Jakumeit
- +49 241 8098032
- j.jakumeit@access-technology.de
From simulation to the digital twin
Right from the start in the 1980s, Access was involved in the development of computer simulation of metal production processes. While the simulation was initially limited to thermal processes, since 2004 the focus of development has been on the fully coupled simulation of mold filling, solidification and distortion. The commercial casting simulation program STAR-Cast was developed together with the partner CD-adapco. In 2016, CD-adapco was acquired by Siemens and STAR-Cast became part of the STAR-CCM+ flow solver from Siemens PLM.
Access focuses on developing new simulation methods and supporting industry by mapping, analyzing and optimizing their production processes. To this end, Access uses STAR-CCM+, Magmasoft and Abaqus and maintains close partnerships with Siemens PLM and Magma. Additive manufacturing of metallic components is a new and growing field of work.
The main areas of application are: Investment casting, die casting, continuous casting, additive manufacturing, thermal processes and complex metallic flow processes (see below)
Focus on applied process simulation in the field of metallurgy
Investment casting
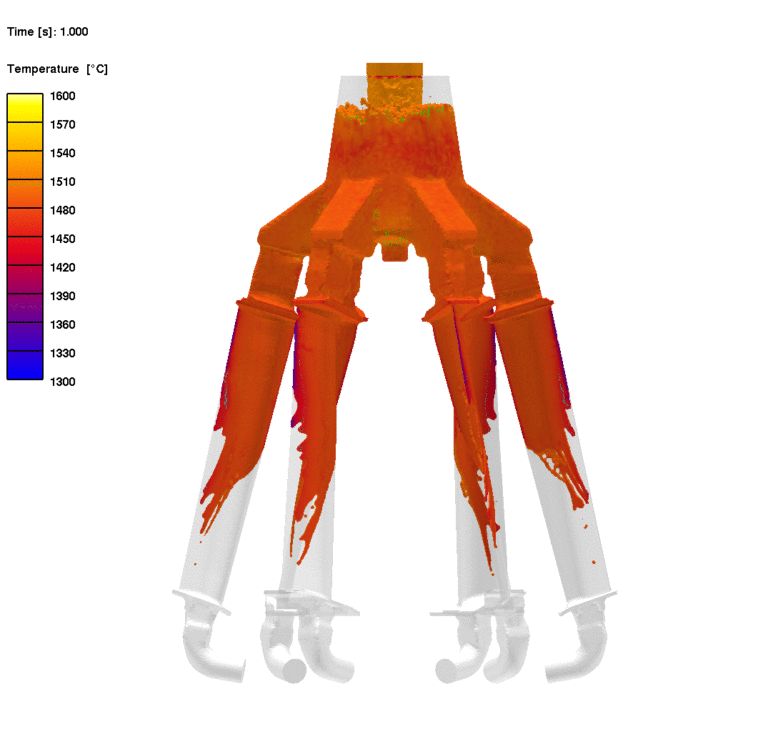
Investment casting has been a focus of process simulation at Access since the mid-1980s. Various investment casting processes can be described numerically:
- Gravity casting
- Centrifugal casting
- Bridgman method
- Fastcast process
The strengths of simulation with STAR-CCM+ and a possible link to Abaqus are:
- Cross-linking, shell generation
- Preheating, heat treatment
- Mold filling, cold run prediction
- Solidification behavior, microstructure formation
- Residual stresses & distortion,
- Shrinkage formation, porosity
Current application examples are
- Centrifugal casting of turbine blades and turbocharger wheels
- Bridgman process for turbine blades and phase change materials
Thanks to the cooperation with CD-adapco (now Siemens PLM) and the experience gained from centrifugal casting as an investment casting process, die casting and gravity die casting were added as a new focus. Here we deal with:
- Cold chamber and hot chamber process
- Hybrid casting
- Low and counter pressure casting
STAR-CCM+ is primarily used as a solver with the strengths in the description of:
- Loading, pouring chamber filling
- Shot, reprint, cold run prediction
- Air pockets, porosity
Examples of applications are
- Vehicle structural frame
- Gearbox, engine block
- Battery tray
Die casting
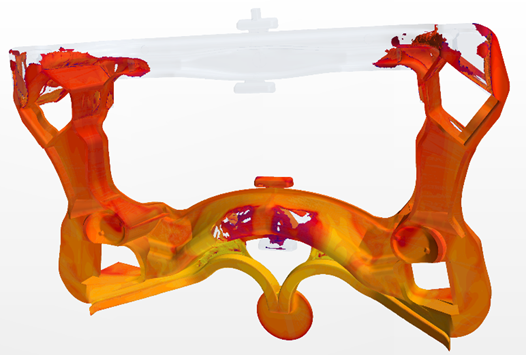
Continuous and semi-continuous casting processes can be mapped with different simulation programs depending on the problem.
MAGMA CC and STAR-CCM+ are available as well as Abaqus for voltage calculations.
- Design and optimization of tundish and launder to improve flow conditions
- Flow conditions at the immersion nozzle (SEN)
- Thermal design/optimization of the die
- Optimization of the overall process (e.g. determination of the sump profile, optimum casting speed, adapted secondary cooling)
- Temperature and speed fields during start-up
- Calculation of the stress distribution in the strand and mold as well as stress-relevant quality criteria
STRANGGUSS
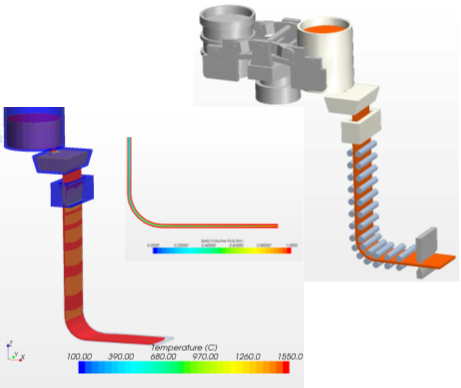
Additive manufacturing
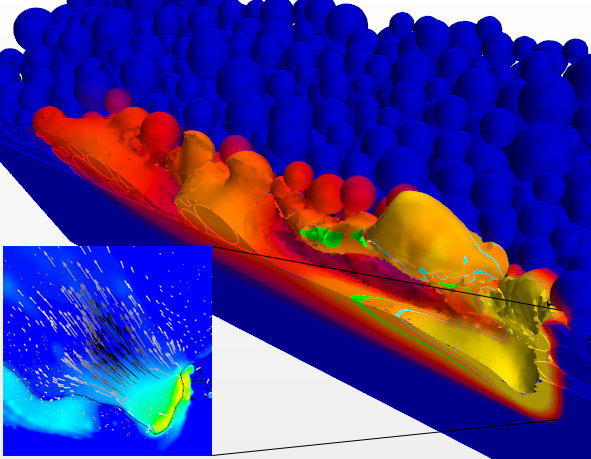
Since 2017, Access has also been working on the additive manufacturing of metal parts using particle-resolved simulation of the processes in the melt pool. The focus here is on:
- Powder Bed Fusion – LPBF/EPBF (Selected Laser Melting – SLM)
- Direct Energy Deposition – DED, Liquid Metal Deposition- LMD
The focus of the simulation is on:
- Particle-resolved process simulation
- Solidification conditions, microstructure parameters,
- Tension and distortion,
- Metal evaporation, keyholing, bonding defects, porosity
Example applications are:
- LPBF of IN718 and Ti6Al4V powder
- LMD from IN718 wire to steel
In addition to special shaping casting processes, we also deal with general thermal processes of various materials. Thanks to the flexibility of STAR-CCM+, the test environments can be mapped in addition to the processes in the material itself and further material properties can be derived via the link to other software (Abaqus, Micress). We simulate in particular:
- Simulation of the thermal environment (oven),
- Heat flows through conduction, radiation and convection
- Solidification conditions
- Bridgman method
- Heat treatment
- Quenching
In addition, we consider the coupling to derived phenomena and properties such as:
- Tension and distortion,
- Segregation
- Structural parameters
- Precipitate formation
- Diffusion of doping elements
Application examples:
- Melting and crystallization furnace for volume processes,
- Heat storage for heating electric vehicles
- Radiant heating in a double ellipsoid furnace
- Magnetic shape memory material in the Bridgman process
Thermal processes
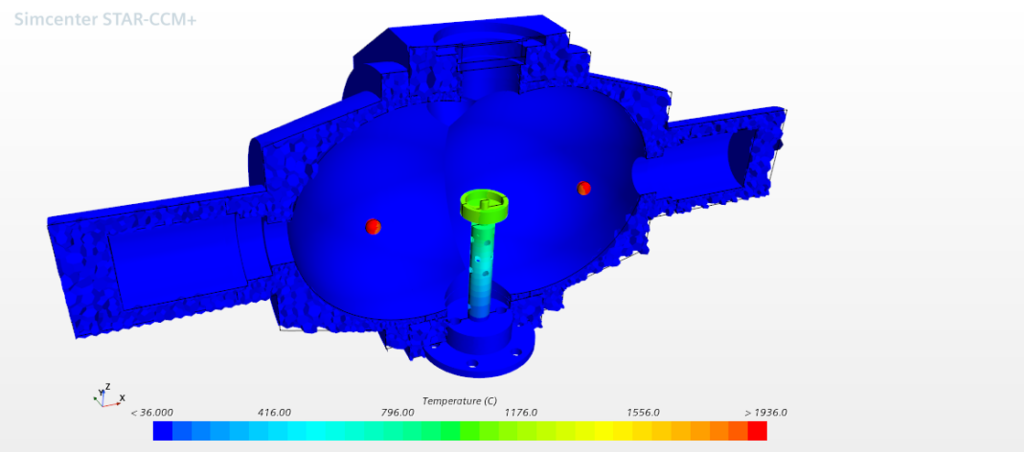
Metallic flow
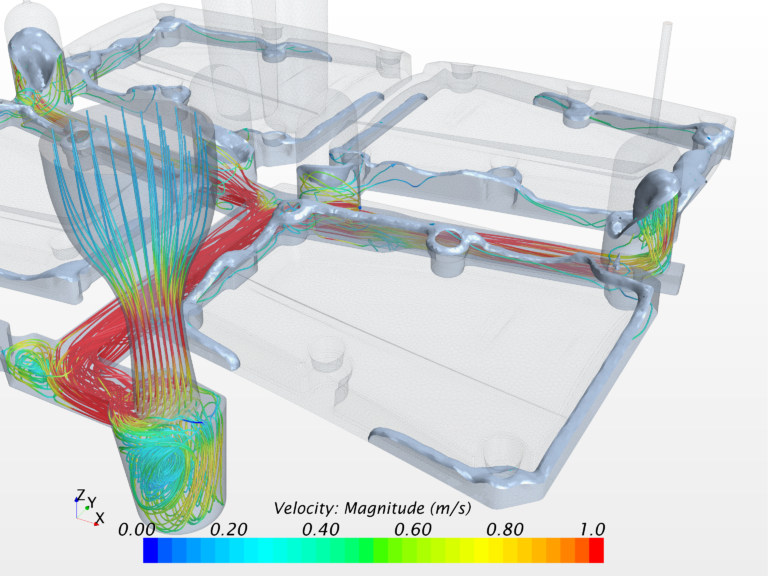
In the run-up to the production of components using casting processes, there are also many purely fluidic issues that we can successfully map and optimize. Typical processes are
- Filling of various systems,
- Melt treatment, inoculation,
- Remelting processes in induction furnaces (VIM) or arc furnaces (VAR)
The use of a universal CFD solver in conjunction with special multiphase models offers the following strengths:
- Complex flow patterns,
- Turbulence models,
- fully coupled temperature distribution and solidification,
- Segregation
Application examples:
- Nano-particle distribution in gravity die casting and sand casting,
- Prediction of slag and foreign particle distribution
- Choke distribution in iron casting,
- Oxide particle deposition and temperature loss in launders.
A digital twin generally refers to a virtual image of a real process. Initially, the digital twin was set to be equal with the simulation of processes, but today the intelligent linking of process data (big data) also plays an important role.
In the design phase, the digital twin is based on simulation data, as the real process does not yet exist. Important here:
- Simulation along the process chain
- Multiscale multiphysics simulation
- Simulation-driven fast replacement models
- Numerical optimization
In the application phase, a lot of measured data is added and intelligent data analysis becomes crucial:
- Data management
- AI models for data analysis
- Data-driven fast replacement models
- Simulation adjustment
- Numerical optimization
Digital twin
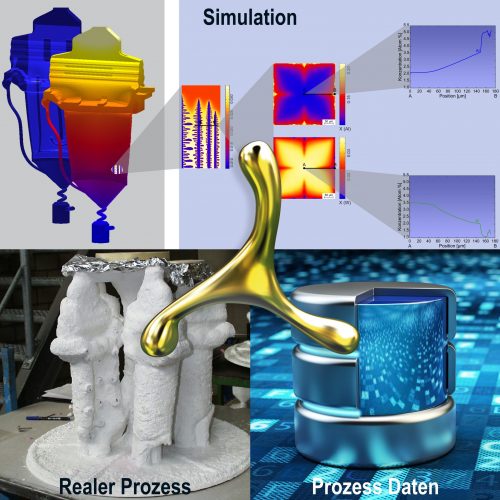
Die Genauigkeit von Gießsimulationen hängt stark von der Qualität und Vollständigkeit der verwendeten Materialdaten ab. Eine qualitativ hochwertige Datenbank wie AMat.Pro spielt eine unverzichtbare Rolle, um hochpräzise Ergebnisse zu erzielen. Mit diesem Webservice können Ingenieure nun direkt über ihren Webbrowser auf den umfangreichen Bestand an validierten Materialeigenschaften von AMat.Pro zugreifen und diese nutzen.
Für jeden, der sich mit Gusssimulationen beschäftigt, ist die Verfügbarkeit genauer und umfassender Materialdaten entscheidend für die Bereitstellung zuverlässiger und vertrauenswürdiger Ergebnisse. Der Zugriff auf AMat.Pro über einen Webservice vereinfacht den Prozess der Integration dieser wichtigen Datenpunkte in Ihre Projekte.